溶接ロボットとは
1. 溶接ロボットとは?
そのままの意味になってしまいますが、溶接ロボットは、今まで人が手作業で行っていた溶接作業を自動で溶接してくれる機械のことです。そもそも溶接に馴染みのない方は多いかと思いますが溶接の歴史はかなり古く、世界をみれば紀元前から青銅器の加工や鉄の接合が行われており、日本でも弥生時代までさかのぼると溶接(青銅器の鋳掛け)とつながります。現代でも溶接は活躍しており、身近な溶接ではビルなどの建物、自動車、電車、航空機、公園にある遊具や遊園地のアトラクションにも溶接は使用されています。中でも高層建築ではスカイツリーが溶接技術で建築されたことで有名ですね。
もはや生活になくてはならない溶接ですが、職人(溶接工)は年中人手不足です。そのため最先端技術の投入には惜しみなく、1960~1970年代から自動車の急激な需要に伴い産業用ロボットが普及、それにつづき溶接ロボットも波及されるようになりました。
溶接は融接、圧接、ろう接の3種類に分類されますが、融接に分類される「アーク溶接」のロボットが一般的に普及されています。
- 融接:溶接材料をガス炎などの熱源で溶融し熱を冷まして凝固させ接合する。
- 圧接:材料と材料の面を密着させ接合部に機械的圧力を加えて金属融合させる。
- ろう接:母材よりも低い融点の金属材料を溶融させ、毛細管現象により接合面の隙間に行き渡り接合する。
アーク溶接とは、アークと呼ばれる放電現象の熱を利用し剛材を溶融し接合する方法です。溶接工が溶接マスクをかぶり溶接棒の先からバチバチ火花が散っている映像がイメージしやすいかと思います。アーク溶接は鉄剛同士やアルミニウム、チタンなどの金属同士の接続、鉄骨フレームや自動車・電車・航空機・船舶などの大型機械の接続でよく使用され、ほぼすべての金属構造物に適用されます。アーク溶接のほかにも、YAG溶接、MAG溶接、MIG溶接、TIG溶接、スポット溶接、レーザ溶接などさまざまな種類の溶接ロボットが現存しています。
- MAG溶接、MIG溶接、TIG溶接:アーク溶接の一種。スポット溶接:圧接の一種、自動車などの車体溶接で使用されることが多い。
- レーザ溶接:レーザー光を照射して剛材を融解して接合する。
1-1. 溶接ロボット使用事例
建設業界
鉄骨柱などの厚い金属を加工するには相当な技術が必要なため、なり手が非常に少ないです。しかし大型の鉄骨柱が必要な高層ビルの需要はどんどん増えています。技術者不足を解消すべく、溶接ロボットの導入が行われています。溶接ロボットの場合、溶接条件を自動算出し正確に自動溶接を行うことができます。クオリティを一定に保ちながら熟練技術者と同品質の作業が可能となります。
自動車業界
自動車の製造に際し、溶接のみならず産業用ロボットや協働ロボットが多様な工程をこなしています。(プレス、塗装、組み立てなど)
自動車製造において溶接は、主に部品や車の骨組みフレーム、車のボディやマフラーなどにおいてアーク溶接とスポット溶接が用いられます。1台あたりおよそ数千カ所ある溶接部分を溶接用多関節ロボットが溶接していきます。重労働かつ技術を要する溶接作業をロボットが行うようになったことにより、生産スピードの向上や人の過酷な作業と健康被害の減少、正確な溶接や溶接時間によるクオリティの確保ができるようになりました。
鉄道・造船・航空・宇宙界
鉄道では台車の枠、部品付け、車両のブロックごとなどに溶接ロボットが適用されています。造船では組立溶接やブロックのアーク溶接システムなど、航空業界ではエンジン部品や組立など多岐にわたり溶接ロボットは活躍しています。
今までの溶接ロボットは産業用ロボットが主でしたが、協働ロボットの普及により、自動化やロボットの設置が難しかった作業も簡単に設置・導入ができるようになりました。それにより作業の効率化と作業者の安全、技術者不足の解消が可能となっています。
(産業用ロボットは安全対策のため人と隔離し安全柵を設ける必要がありました。協働ロボットは人と作業することが目的として作られたため安全設計がされており、安全柵が不要で省スペースに設置ができ、産業用ロボットよりも複雑な工程が可能です。)
1-2. 溶接ロボットのメリット・デメリット
メリット
- 従業員の健康や安全を守れる
溶接ロボットは今まで人が行っていた手作業の溶接を、自動で溶接できる機能を持つロボットです。今まで人が作業をする場合、溶接ヒュームなどの粉塵や有害物質による健康被害の危険を伴っていましたが、溶接ロボットが代替するようになれば従業員の健康と安全を守れるようになります。 - 人手不足解消
少子高齢化にともない溶接業界だけでなく製造業全体で人手不足が起きています。溶接業界では技術者の高齢化により継承者不足が深刻です。溶接ロボットはティーチング(溶接ロボットに対し作業を覚えさせる工程)をする必要がありますが、一度作業を覚えさせてしまえば24時間稼働させることが可能なため手作業であったときよりも生産力が大幅に向上します。また、溶接ロボットは一度作業を覚えさせれば技術の再現性が高いです。そのため属人化しやすく継承者がいない作業に対しても安全性を保ちながら生産を行うことができます。そして作業負担の分配が可能になれば、熟練の技術者を別の高付加価値業務に集中させることができるため、効率化・利益化につながります。 - 品質と作業時間の改善
さきほど溶接ロボットは一度作業を覚えさせれば技術の再現性が高いと記載しましたが、溶接ロボットはパラメータ設定、ティーチング、センシング、条件など初期設定に手間がかかる分不備なくセットアップが完了すれば作業がデータとして保管され、溶接個所の忘れや技術のムラもなく均一な作業で安定した品質が生産可能となります。また一定のスピードを保って作業ができるため進捗管理がしやすく、生産管理がしやすいため全体の工期に余裕を持たせることができます。
デメリット
- 導入費用がかかる
溶接ロボットの導入にはロボット本体に加え、作業内容によりエンドエフェクタやコントローラなどの周辺機器、複雑なロボットのセットアップであればSIerに依頼する必要がありその費用もかかります。初期費用だけでなく、定期的なメンテナンスや消耗品の交換などもあり、ロボットが故障した場合や修理費用などの考慮も必要です。しかし、一度導入してしまえば人手不足解消や生産力・品質の向上、生産管理などの管理も容易となります。長期的にみて、投資した費用に対し得られる利益が試算できた場合、導入を検討してみてもよいかもしれません。導入に際し、補助金制度について参照してみるのもおすすめします。 - 自動化させるための知識が必要
溶接ロボットの導入には溶接の知識はもちろん、ロボットを動作させるためのティーチングとプログラミングの知識・技術が必要となります。ロボット制御と設計、溶接の知識の異なる技能が必要なため、溶接作業者とロボットSIerが協力してロボットをセットアップすることが多いかと思います。
ロボットは初期設定したパラメータ設定や条件、ティーチングに基づき作業するため、初期設定の際不備があれば不良品が生産されてしまいます。ですので、SIerにセットアップを依頼した場合でも作業内容に応じた調整や変更、ティーチングの知識が多少でも必要となります。しかし、協働ロボットであればプログラミングが必要なくロボットを直接動かすことで動作を覚えさせることができるため、単調な作業であればプログラムを組む必要なくティーチングが可能となります。
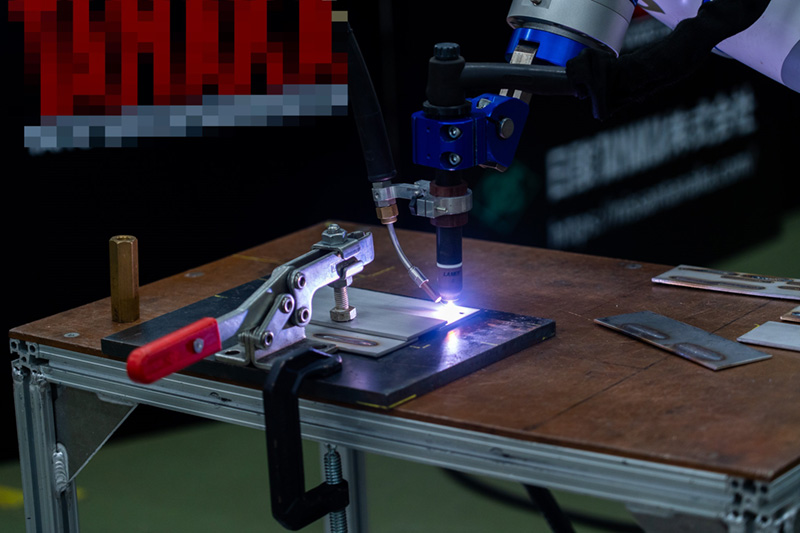
おすすめロボット紹介
「DOBOTARC」は従来の産業溶接ロボットのような安全柵が不要で、省スペースに設置ができる移動式の協働型溶接ロボットです。
世界的協働ロボットメーカーDOBOTの正規一次代理店である【株式会社フレアオリジナル】がSIerとしての経験を活かし、産業用溶接ロボットの使い勝手と現場の意見を取り込み完成しました。業界では珍しいフィラーワイヤー付きTIG溶接が可能にもかかわらず、比較的安価に導入できます。2024年にはハンディーレーザー溶接をDOBOTロボットに持たせたDOBOT Laserパッケージもリリースされ、高速かつ高出力でゆがみの少ない高品質な溶接が可能となります。